The Essential Guide to Soldering Iron and Metal Wire
Soldering is a fundamental skill in electronics, allowing individuals to connect components and create circuits. At the heart of the soldering process are two crucial tools the soldering iron and solder wire. Understanding how these tools work and their applications is essential for anyone looking to delve into the world of electronic assembly and repairs.
What is a Soldering Iron?
A soldering iron is a hand-held tool used to heat metal to a temperature that allows solder to flow and create a secure electrical connection between components. The iron consists of a heated metal tip and an insulated body. The tip, usually made of copper, is designed to withstand high temperatures, often reaching up to 400 degrees Celsius. Different types of soldering irons exist, ranging from simple handheld models to more advanced temperature-controlled units.
Choosing the right soldering iron is crucial for successful soldering. For beginners, a basic, inexpensive soldering iron with a power rating between 20 to 30 watts is often sufficient. Those working on more complex projects may benefit from a higher wattage iron or a temperature-controlled model to provide precise heat management.
The Role of Solder Wire
Solder wire is the metal that joins two or more electronic components together. It typically consists of a mixture of tin and lead, though lead-free options have gained popularity due to health and environmental concerns. Lead-free solder often contains a combination of tin, silver, and copper. The choice of solder wire can affect the quality of the connection and the overall durability of the assembly.
When selecting solder wire, you’ll encounter different diameters, usually ranging from 0.5mm to 1.0mm. For intricate work with small components, thinner solder wire is recommended. Conversely, for larger connections, thicker wire may be more appropriate. Additionally, the flux core in solder wire helps the solder melt and flow better, ensuring a clean connection with minimal oxidation.
Techniques for Effective Soldering
Soldering requires technique, patience, and practice. Here are some essential steps to ensure effective soldering
soldering iron metal wire
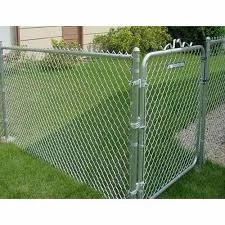
1. Preparation Start by cleaning the surfaces to be soldered. Removing oxide and dirt ensures a strong bond. For this, a fine-grit sandpaper or isopropyl alcohol can be effective.
2. Heat the Iron Preheat your soldering iron. A properly heated iron is vital for melting the solder quickly and efficiently.
3. Apply the Solder Touch the solder wire to the joint while simultaneously applying the soldering iron tip. The heat will melt the solder, allowing it to flow into the connection.
4. Remove and Let It Cool Withdraw the solder and then the iron, allowing the joint to cool by itself. Avoid moving the components while the solder is cooling to ensure a solid connection.
5. Inspect the Joint A good solder joint should be shiny and smooth, indicating a strong connection. If it appears dull or has a rough texture, it may need to be re-soldered.
Safety Considerations
Working with soldering irons involves safety precautions. Always work in a well-ventilated area, as fumes from melted solder can be hazardous. Additionally, always wear safety goggles to protect your eyes from splashes and keep the soldering iron in a safe place to avoid burns.
Conclusion
Soldering is an invaluable skill for electronics enthusiasts, allowing them to create and repair circuits with precision. By mastering the use of soldering irons and solder wire, individuals can embark on projects ranging from simple repairs to complex builds. With practice and attention to safety, one can develop proficiency in this essential craft, contributing to the vast world of electronics.