MIG Welding Cast Iron with Stainless Wire A Comprehensive Guide
MIG (Metal Inert Gas) welding, also known as Gas Metal Arc Welding (GMAW), is a popular welding process due to its versatility and efficiency. One of the challenging materials for welding is cast iron, which is known for its brittleness and thermal conductivity. Traditionally, welding cast iron requires special techniques and filler materials, but many welders are exploring the use of stainless steel wire for MIG welding cast iron. This article aims to provide insights into this innovative approach.
Understanding Cast Iron
Cast iron is a group of iron-carbon alloys with a carbon content greater than 2%. It is favored in various industrial applications due to its excellent castability, wear resistance, and machinability. However, its high carbon content leads to challenges when welding; it can be prone to cracking and may require preheating and post-weld heat treatment.
Why Use Stainless Steel Wire?
Using stainless steel wire to weld cast iron may seem unconventional, but it has its advantages. Firstly, stainless steel has a higher tensile strength compared to traditional cast iron filler wires. This can be beneficial for applications requiring greater durability. Secondly, stainless steel provides better corrosion resistance, making it an ideal choice for components exposed to harsh environments.
Preparation for MIG Welding
Before you start welding, proper preparation is crucial. Here are the steps to follow
1. Clean the Surface Remove any paint, rust, and dirt from the casting surface using a wire brush or grinder. A clean surface ensures better adhesion of the weld.
2. Preheat the Workpiece Preheating the cast iron is essential to reduce the risk of cracking due to thermal stress. Heat the joint area to around 400°F (204°C) using a propane torch or an oven. Be careful not to overheat, which can change the metallurgy of the cast iron.
mig welding cast iron with stainless wire
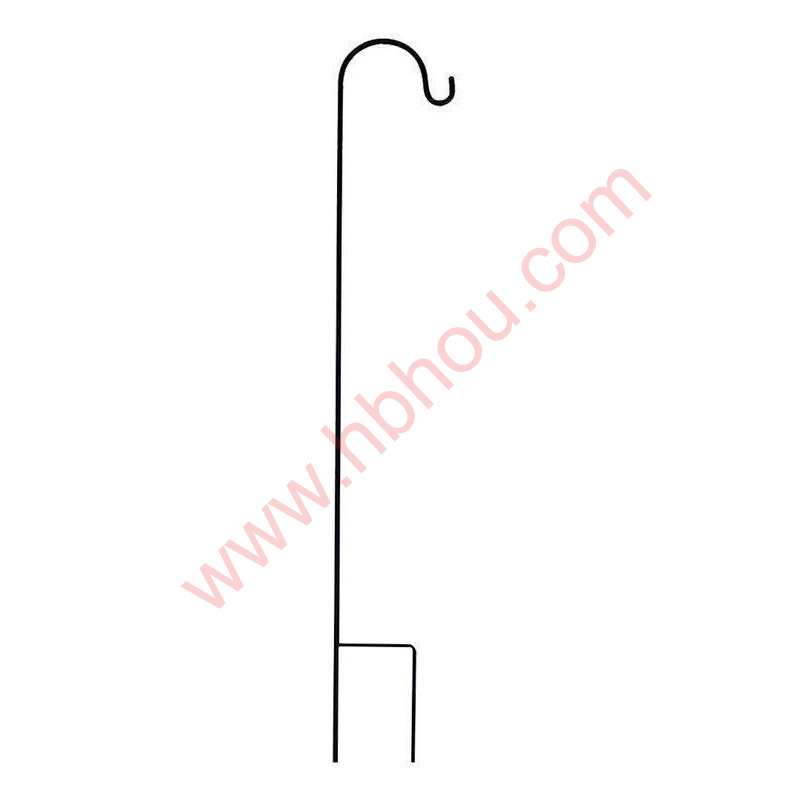
3. Choose the Right Wire Select a stainless steel MIG wire suitable for your application. Common choices include ER308L and ER309L, which offer good mechanical properties and corrosion resistance.
4. Setting Up the Welder Ensure your MIG welder is set up for gas shielding, typically with Argon or a mix of Argon and CO2. Set the voltage and feed speed according to the specifications for the stainless steel wire.
Welding Technique
1. Tack Weld Start by creating small tack welds at intervals along the joint. This helps maintain alignment and prevents warping.
2. Welding Pass Use a stringer bead technique, moving steadily and avoiding excessive weaving. This minimizes heat input and helps control the weld pool, reducing the risk of cracking.
3. Control Heat Input Monitor your heat input closely. Too much heat can lead to thermal distortion or even cracking in the base metal.
4. Post-Weld Treatment Once welding is completed, let the joint cool gradually to room temperature. Depending on the application, post-weld heat treatment may be necessary to relieve residual stress and improve the weld's properties.
Conclusion
MIG welding cast iron with stainless steel wire offers a viable alternative for welders seeking to enhance strength and resistance to corrosion in their projects. By understanding the properties of cast iron, using the appropriate techniques, and following proper preparation steps, welders can achieve high-quality, durable welds. As with any welding process, practice and experience will lead to better results, making experimentation with different techniques and materials worthwhile.