MIG Welding Cast Iron with Stainless Wire A Comprehensive Guide
MIG (Metal Inert Gas) welding has become a popular technique for joining various metals due to its speed and versatility. One of the less commonly discussed applications is MIG welding cast iron using stainless steel wire. This approach can offer significant advantages, especially in repair and restoration projects.
Cast iron, known for its excellent castability and machinability, presents unique challenges when welding. Its high carbon content makes it prone to cracking, especially when subjected to rapid cooling. Traditional methods often recommend using nickel-based electrodes for welding cast iron. However, employing stainless wire can provide an alternative for those looking to utilize MIG welding processes.
One of the primary reasons for using stainless steel wire is its superior ductility and corrosion resistance compared to traditional electrodes. When welding cast iron, stainless wire can establish a robust joint while minimizing the inherent brittleness associated with cast iron. Electrode selection plays a crucial role in achieving the desired weld characteristics. Typically, ER308L stainless steel wire is favored for its excellent elongation and impact resistance.
Before starting the welding process, proper preparation of the cast iron pieces is essential. Begin by cleaning the surfaces to remove any contaminants such as rust, oil, and dirt. A clean surface ensures better penetration and bonding of the weld metal to the base material. Additionally, preheating the cast iron to around 300°F (150°C) can help reduce the thermal shock and minimize the risk of cracking during the welding process.
mig welding cast iron with stainless wire
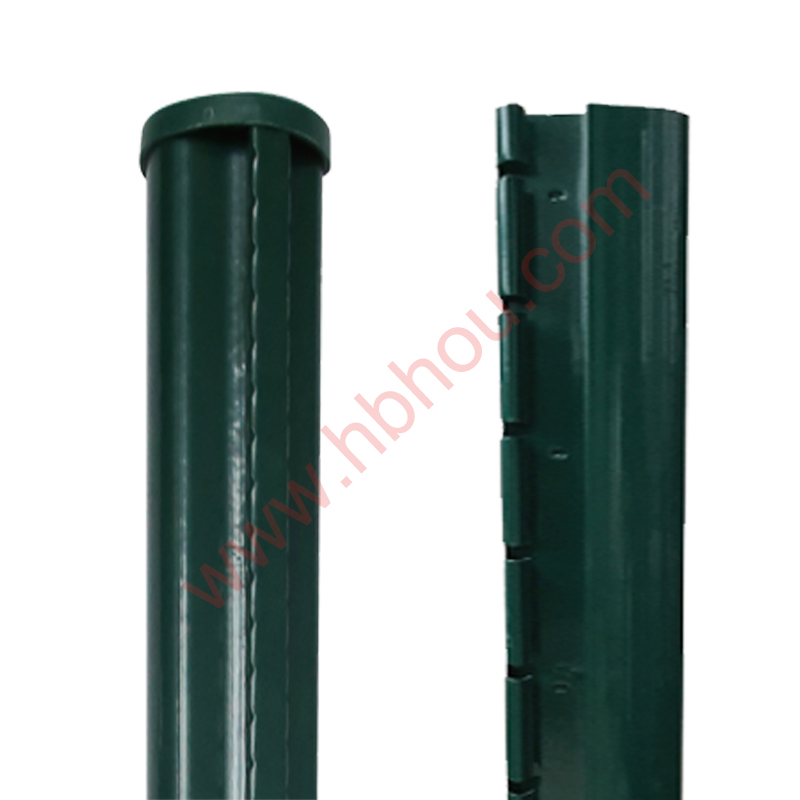
MIG welding cast iron requires careful consideration of parameters such as voltage, wire feed speed, and travel speed. Maintaining the appropriate arc length and avoiding excessive heat input is crucial to prevent warping or distortion of the cast iron. A short arc length and a quick travel speed can aid in reducing heat buildup in the base material.
Another technique to enhance the weld quality when using stainless wire is the use of a suitable shielding gas. A mixture of Argon and CO2 is commonly used, providing excellent arc stability and weld bead appearance. The ratio can vary; however, a 75% Argon and 25% CO2 blend often yields good results.
Post-weld treatment is equally important. Allow the weld to cool slowly to minimize stress and potential cracking. Using a slow-cooling blanket or sand can help maintain a stable cooling rate.
In conclusion, MIG welding cast iron with stainless wire is a viable method for achieving strong, durable joints. By carefully preparing the workpieces, selecting the right materials, and controlling the welding parameters, welders can successfully navigate the challenges of cast iron welding. This technique not only enhances the repairability of cast iron components but also extends their service life, making it a valuable skill in any welding repertoire.